While it’s generally a best practice to keep foundry tool designs simple, some castings are impossible to achieve without introducing some complexity. Often, that complexity comes in the form of water cooling.
If you need to spot-cool heavy sections, or if your mold is staying too hot for too long — leaving you with shrinkage, porous castings, or aluminum soldering tears — water cooling might be worth looking into.
So, let’s explore what you need to know about the technique. Specifically:
• When you should use it
• How it works
• Challenges you may face
• Considerations for your foundry
Signs you should consider water cooling
While it’s best to start simple with your cooling techniques, sometimes you need a method that packs a bigger punch. In fact, about half the molds we build utilize water cooling.
Here are a few factors that may indicate water cooling will be the most effective way to cool your mold and casting.
- Cycle time. If your foundry has rapid target cycle times, chill pins or air cooling alone might not be enough to effectively cool your mold and casting at the desired rate.
- Production rate. Similar to a rapid cycle time, the higher your production rate, the more likely it is you’ll need to use water cooling. For example, if you’re producing a thousand castings per year, you can likely use simpler techniques. But if you’re producing a hundred thousand castings per year, you may need the power of water cooling.
- Complex casting geometry. Big, heavy castings with isolated sections often require water cooling to ensure proper solidification.
Water cooling methods and how they work
Because of how quickly and effectively water extracts heat, water cooling is our preferred cooling technique. It can even be paired with other methods to pack a bigger punch — for example, spot cooling by running water through a chill pin made of dissimilar metal.
Most commonly, our design engineers use bubblers, circuits, and baffles to achieve solidification without defects.
Bubblers
In a bubbler, the water travels up to the tip then circles back around and out the same way it entered. Because the water remains in a confined space with limited surface area, bubblers are not an effective choice for general cooling, but can provide much needed spot cooling for tricky sections, like heavy spots.
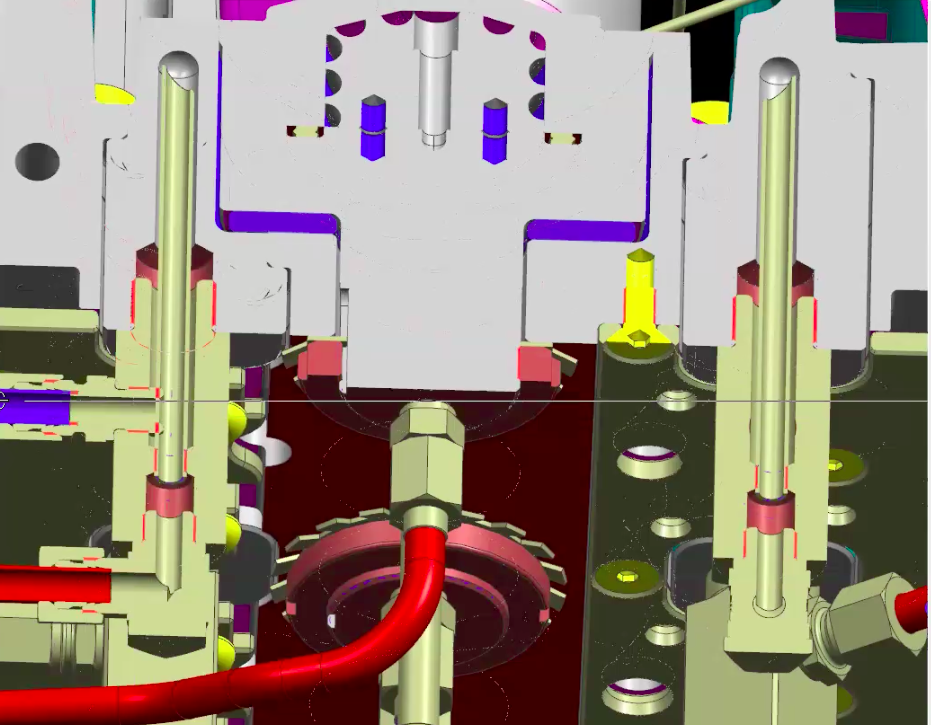
Circuits
In contrast to bubblers, circuits are the most effective and straightforward way to bring the overall temperature of your tool down by cooling large, simple sections of your casting. Wherever you can get a drill into the tool, you can create a circuit.
With this method, the goal is long, straight channels connected by cross-drilled sections that extend across a large swath of the mold. The more surface area a circuit creates, the more effectively the water will extract BTUs from the molten metal.
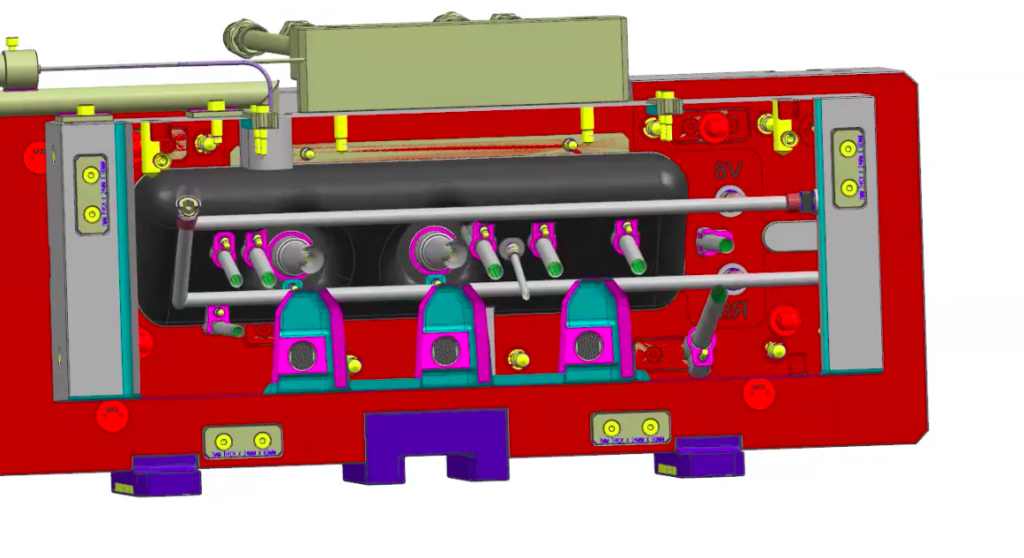
Baffles
Baffles are a type of circuit that redirect water to create more surface area in a smaller segment of the mold, rather than allowing it to follow a straight path across a larger distance. When using this type of method, our design engineers prefer to add spiral baffles — they deliver the highest cooling rate in the lowest amount of space.
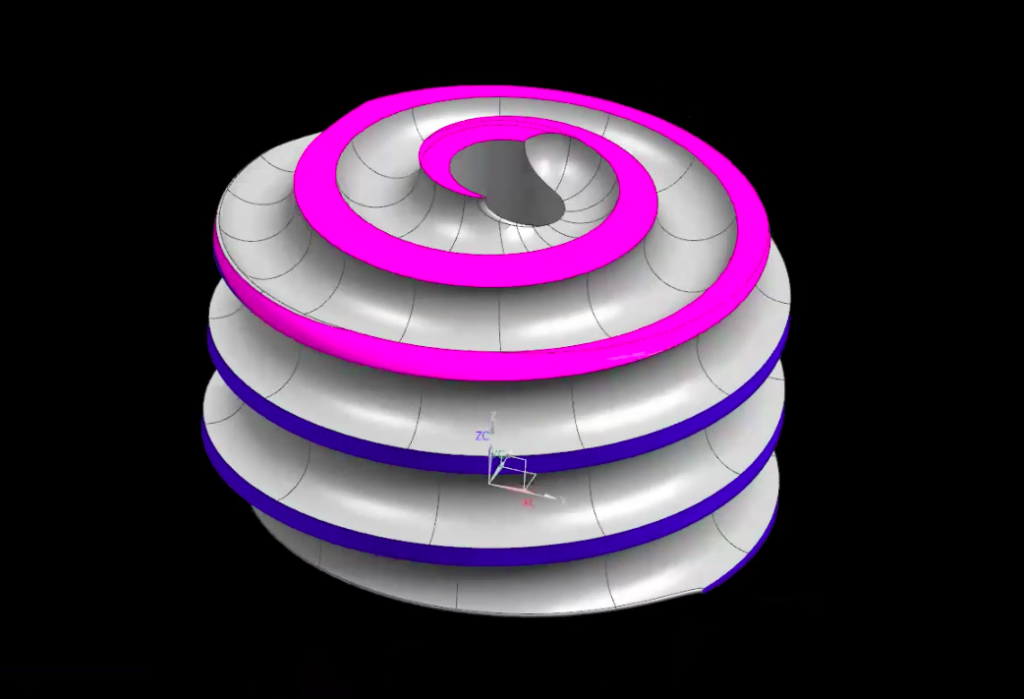
Water cooling challenges
While the most effective form of cooling, water cooling is also the most challenging — with more moving pieces than other techniques, there’s more room for things to go wrong. But our team of experts is here to ensure things go right.
Complex casting geometry limits available space
Typically, larger castings require more intense cooling methods — after all, there’s more material to solidify. Adding water cooling features can make an already complex mold geometry even more challenging. When designing your mold, here are a few questions we consider to ensure that water cooling truly is the best option for your needs.
- Is there enough space in the tool for all the bubblers, baffles, circuits, plumbing lines, and other features you need to effectively cool your casting?
- Is there enough space for all the backup steel that prevents the water from reaching the molten metal in the event of a leak?
- Is your machine envelope large enough to accommodate a big, heavy mold?
If the answer to any of these questions is no, we will likely try other cooling methods first.
Water and molten metal don’t play well together
Cracks and leaks should be avoided with any mold, especially when water cooling is involved. When water reacts with molten metal, the resulting steam is hot, powerful, and (in the worst case) dangerous for both employees and the casting integrity.
To avoid accidental cracks and leaks, it’s crucial to have a robust mold. This means using quality steel — like a premium H13 — that can stand up to thermal fluctuations. And you’ll want to leave a buffer of least an inch of steel between all water lines and molten metal cavities to ensure that no leaks or cracks develop.
From hand bending steel tubing lines to conducting thorough leak checks, our expert journeymen patternmakers take extra care when finishing and assembling foundry tools. That way, you can be confident that you’ll achieve your solidification goals without risking casting defects.
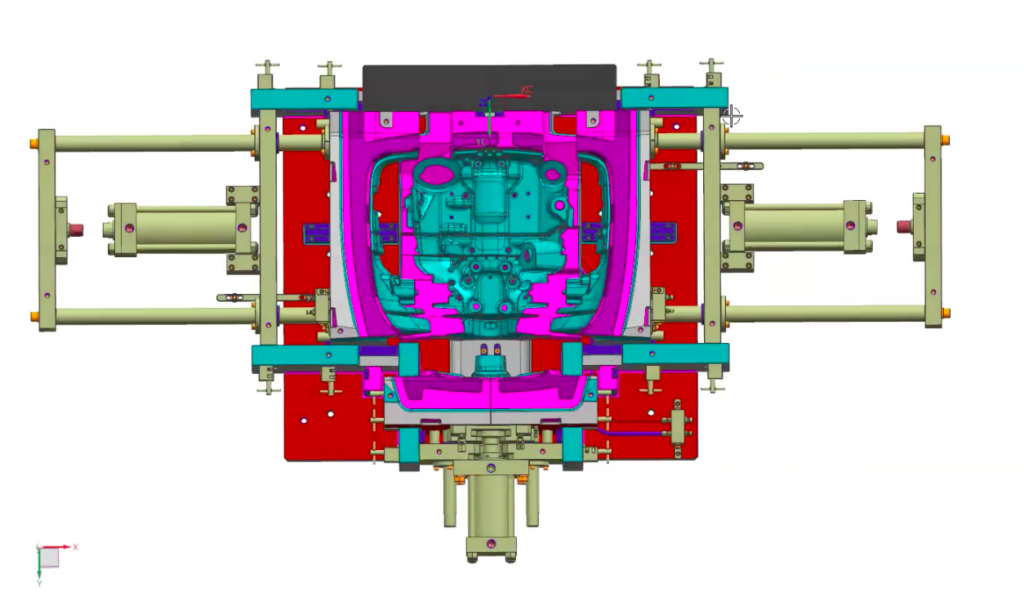
Foundry considerations
One of the biggest factors that determines whether and how we design a foundry tool with water cooling is a foundry’s capability to accommodate those techniques. To effectively use water cooling, foundries must be able to run water lines and commit to a higher level of maintenance.
Water systems vary in complexity and effectiveness
Like mold cooling methods, water systems range from straightforward to highly complex and technical setups. At its most basic, you need two things: A way for water to flow through your tool, and a way to control the flow rate.
Some folks use city tap water from spigot, hook a hose to a block, turn it on, and leave it on. Some have a closed loop system with a chiller that utilizes a PLC-controlled tower with valves to each separate water circuit. Others have something in the middle.
It’s a matter of delivering something feasible. A complex mold does no good without the infrastructure to support it. So, we’ll work to understand your foundry’s capabilities, and to design and deliver a mold that meets your solidification needs and works at your facility.
Additional maintenance needs beyond routine upkeep
When it comes to maintenance, foundries must take a few additional steps beyond traditional mold maintenance practices. This can include conducting regular leak checks, replacing mold sealant around the threads as needed, keeping pumps in good working order, and clearing away hard water buildup in water lines.
Effective water cooling starts with your design… but it doesn’t end there
Implementing water cooling the right way takes more than just foundry mold design know-how — it takes years of experience, careful final finishing, and a deep understanding of your foundry’s goals and situation.
Partner with Anderson Global to build foundry tooling that makes parts right the first time, no matter how complex. Let’s talk about your next tooling project. Get in touch with our team.